Main Equipment
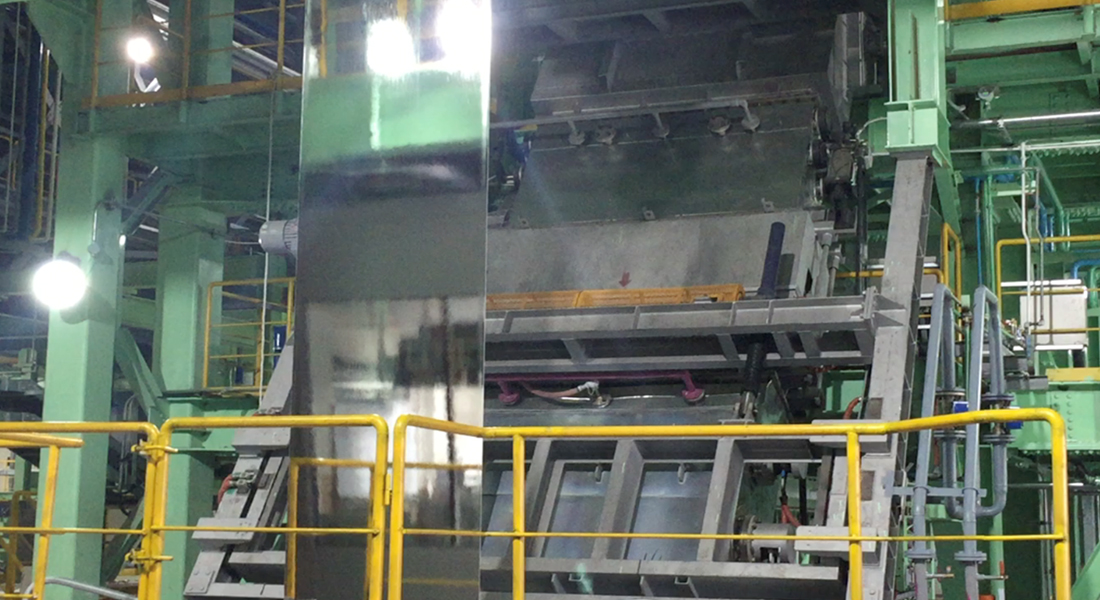
■ Product Description
The purpose of the Continuous Galvanizing Line (CGL) is to apply a coat of zinc onto the surface of steel coil in an effort to increase their corrosion resistance. There is a wide range of Zinc coating thickness control, and the galvanized steel sheets are used for a broad range of purposes, including construction materials, automobiles and electrical appliances.
Advanced Technologies
- Optimized Engineering with More than 30 Years Experience in Operation & Maintenance of POSCO
- Patents for Engineering & Operation of CGL
- Specialized Engineering & Equipment with Operation Know-how (Pre-Treatment, Furnace, POT, Snout, Cooling Tower, SPM, T/leveller, etc.)
Competitive price
- World-wide Global Sourcing Network
- Self-Implementation of Engineering for Specialized Equipment
Smart Schedule & Management
- Standardized Engineering & Manufacturing Management Program
- Experienced Man-Power for Supervision with Maintenance & Operation
■ Main Parts Details
Pre-Treatment
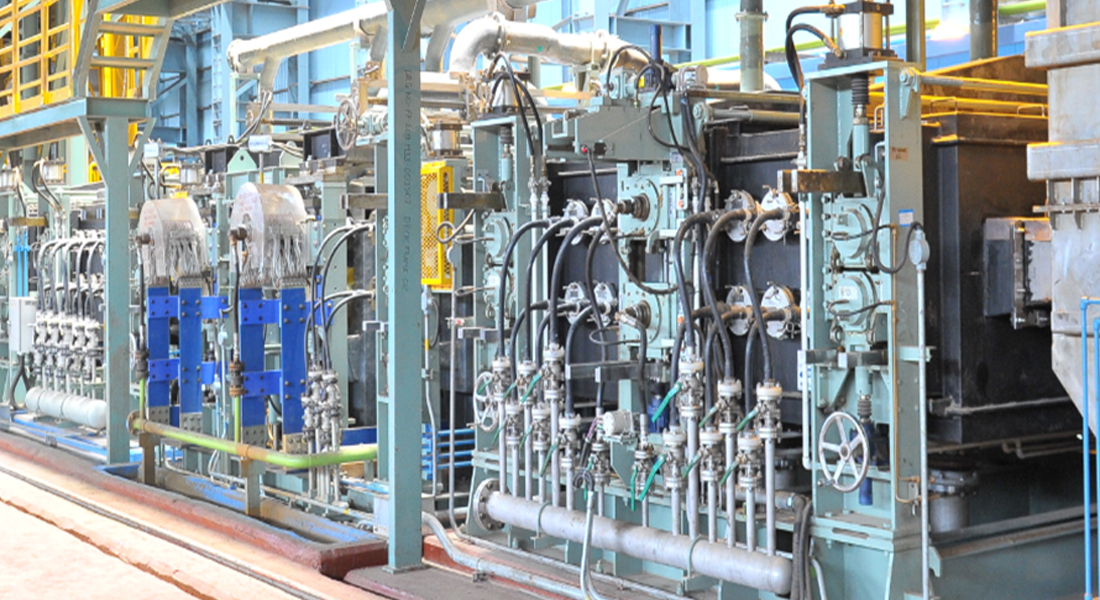
■ Product Description
This cleaning system is a most advanced and integrated system which comprises degreasing unit, No.1 brushing unit, electrical cleaning unit, No.2 brushing unit, hot water rinse unit, and hot air dryer. All these units will be actually designed and manufactured to accomplish good cleaning degree on strip surface, even in case of oxidized strip surface.
■ Main Parts Details
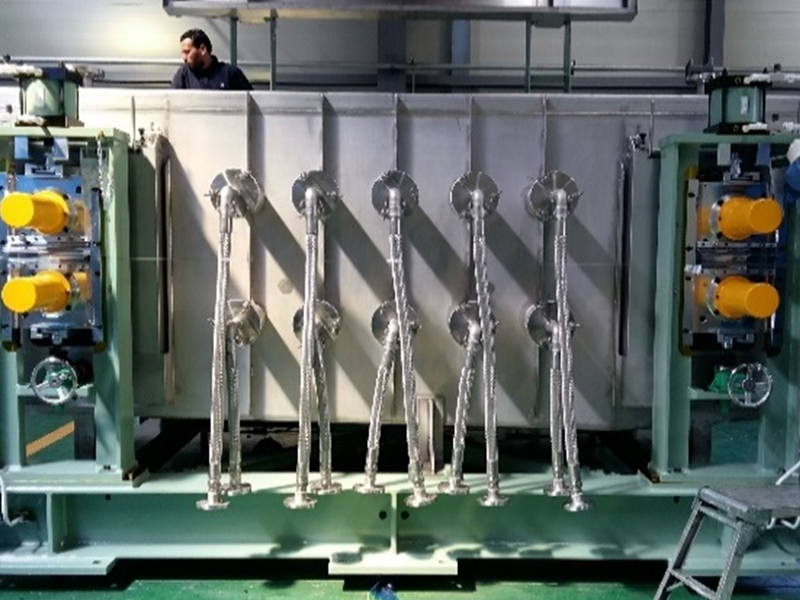
Degreasing Unit
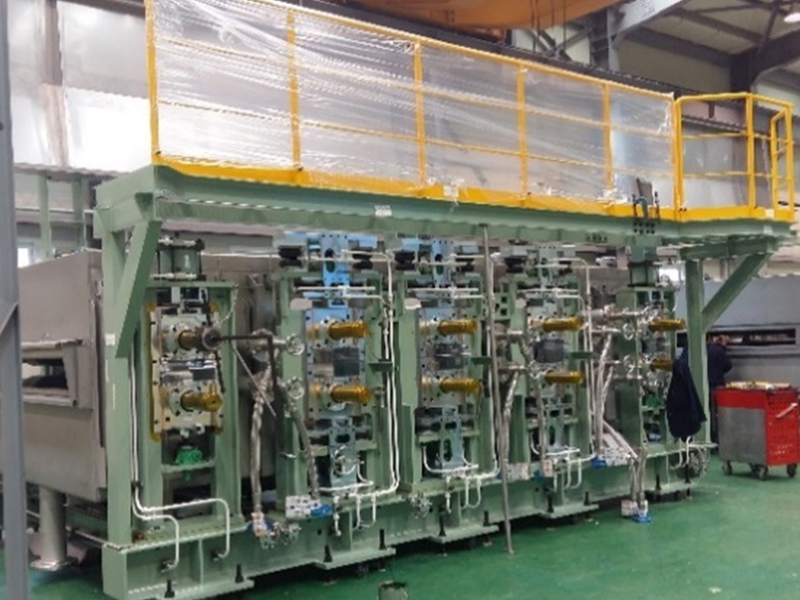
Brushing Unit
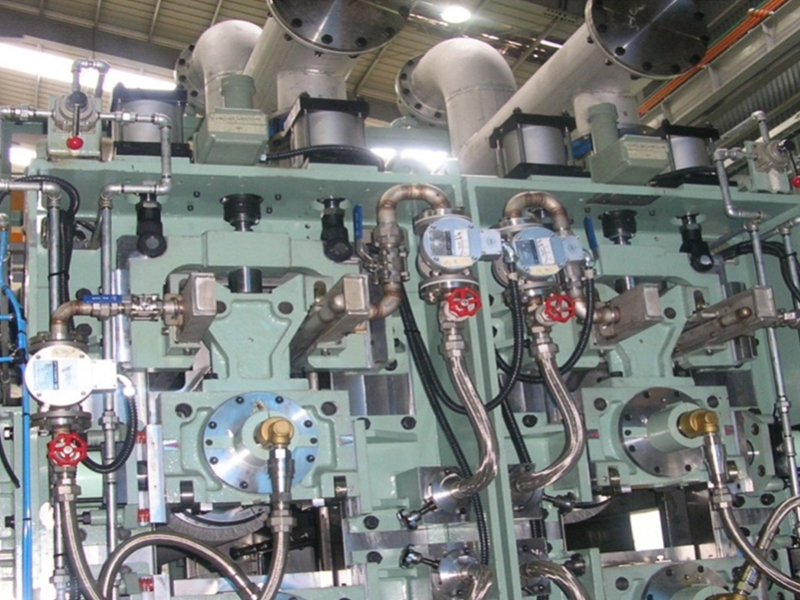
Abrasive Brush Unit
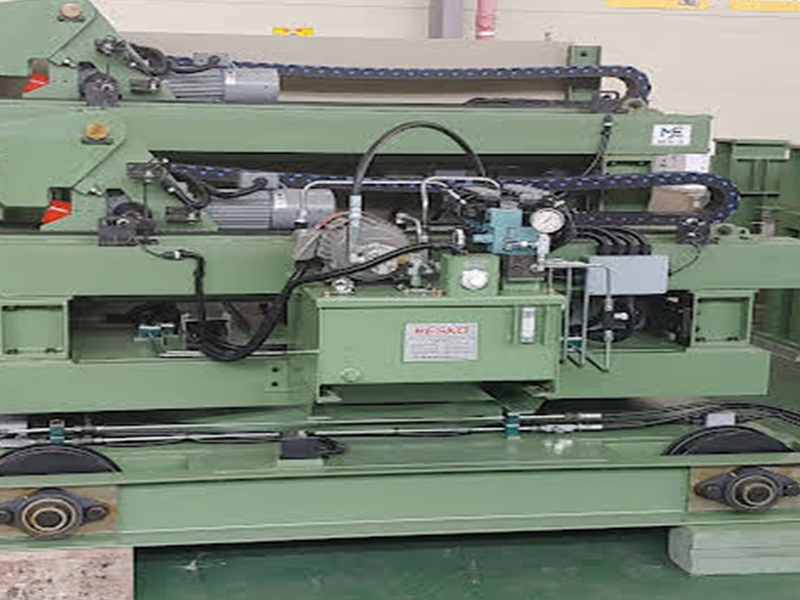
Roll Changing System
Furnace
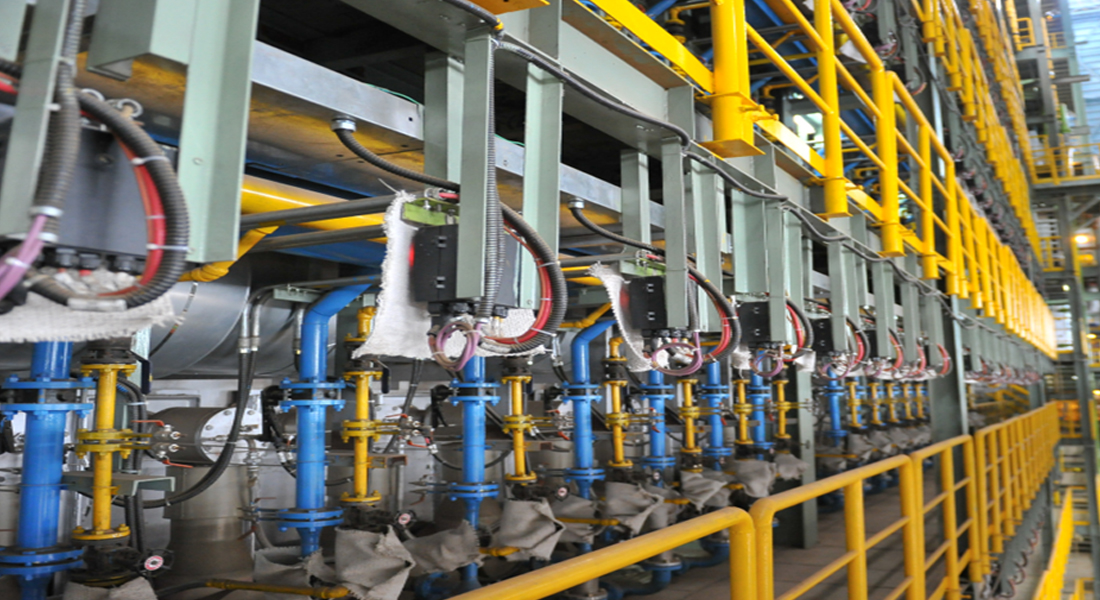
■ Product Description
MJE, with rich technology and experience, have proposed to provide the Furnace of CGL with highly efficient equipment and complementary services including design and supervision for manufacturing, erection, commissioning, and test runs.
New technologies for quality improvement, energy saving, the lessening of public nuisance, labor saving, maintenance and safety are adopted positively to ensure safe and long-term service. Uniform cooling is obtained through special cooling units allowing crosswise gas flow adjustment in several zones to maintain strip temperature homogeneity. The cooling is performed by a first slow cooling section and a rapid/slow cooling section under high content H2 protection atmosphere (5 % up to 40 % H2).
These Furnaces can be of different configuration to suit process requirement. Some of the widely used furnace configurations include
- All Horizontal Configuration
- All Vertical Configuration
- L Shaped Furnace
■ Furnace Lay-Out
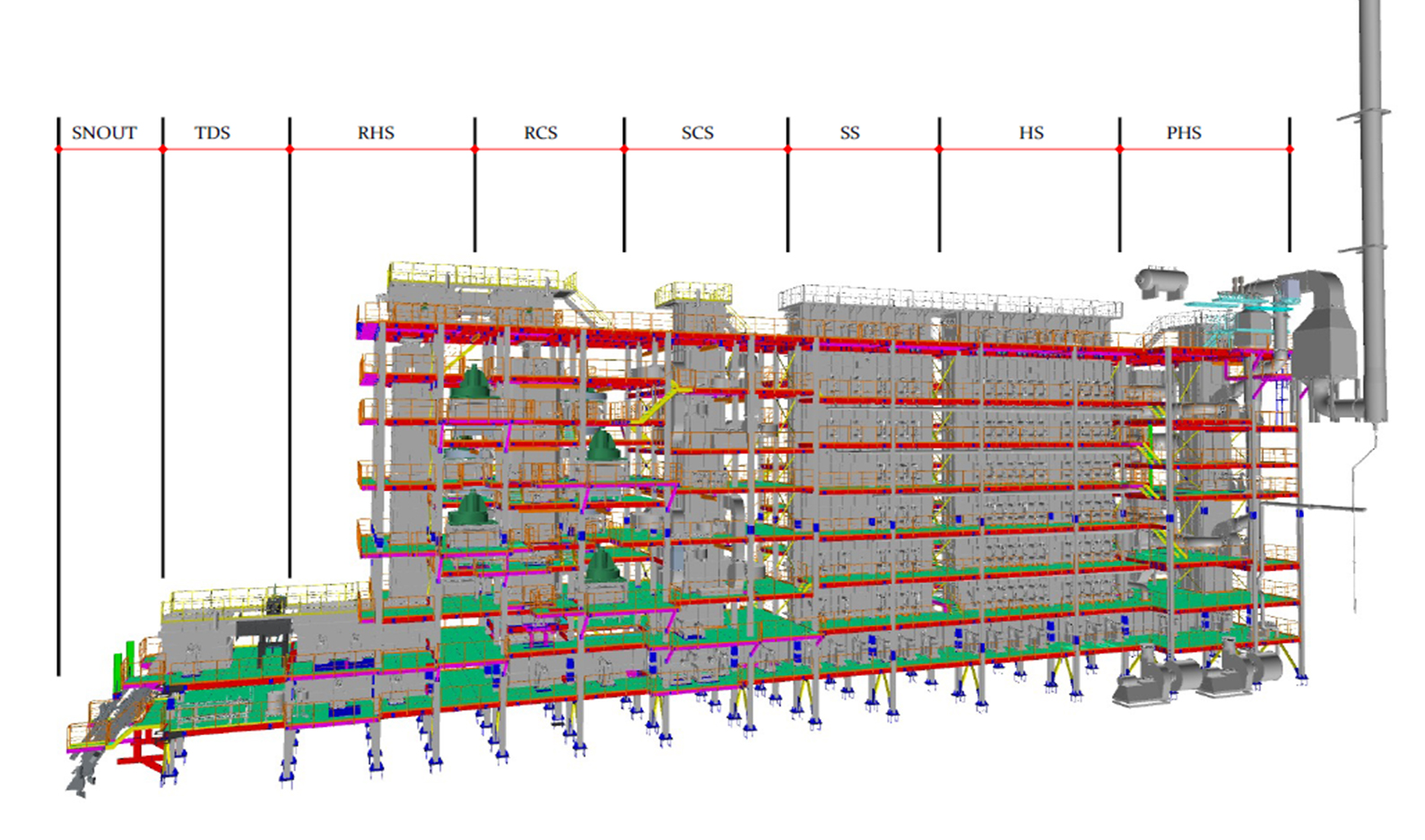
■ Key Feature
Heat Recovery by PHS
- Convection Heating By Exchange With The Waste Exhaust Gas
- Waste Gas Cooled From High Temp. Down To Low Temp.
- Strip Pre Heat
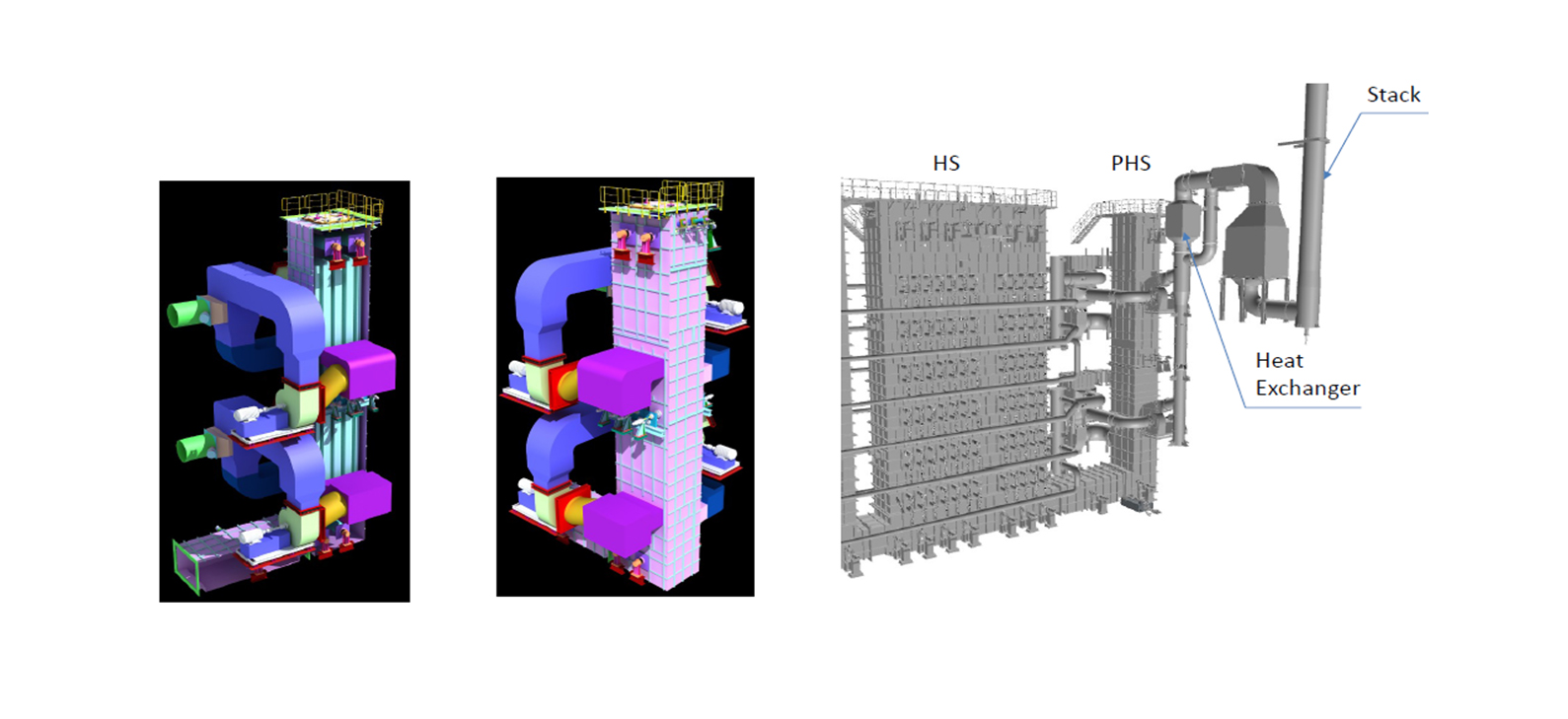
Rapid Cooling Technology
Rapid cooling of > 50℃/sec from 700℃ down to 450℃ up to 1.0mm thick strip @5%H2-H2 ATM.
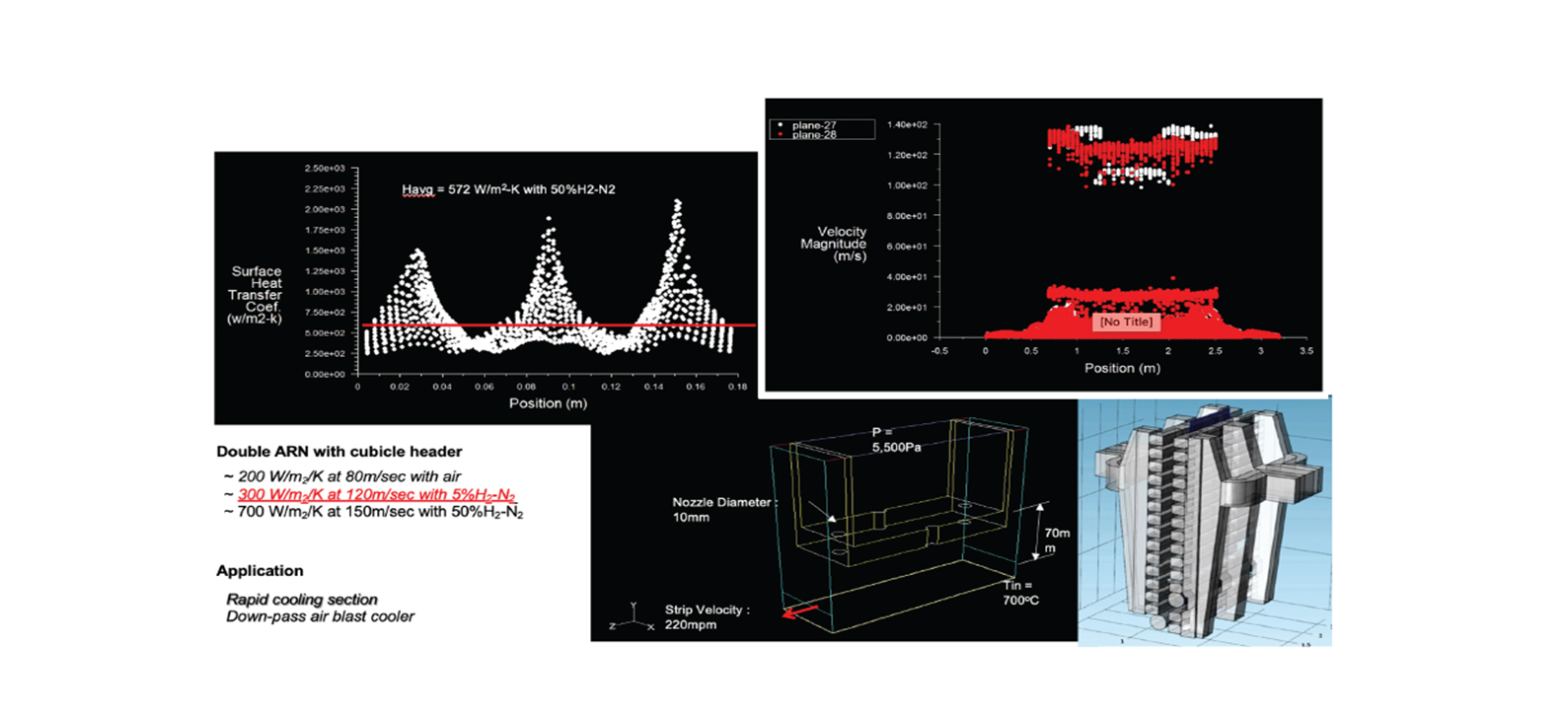
Modular Type Casing
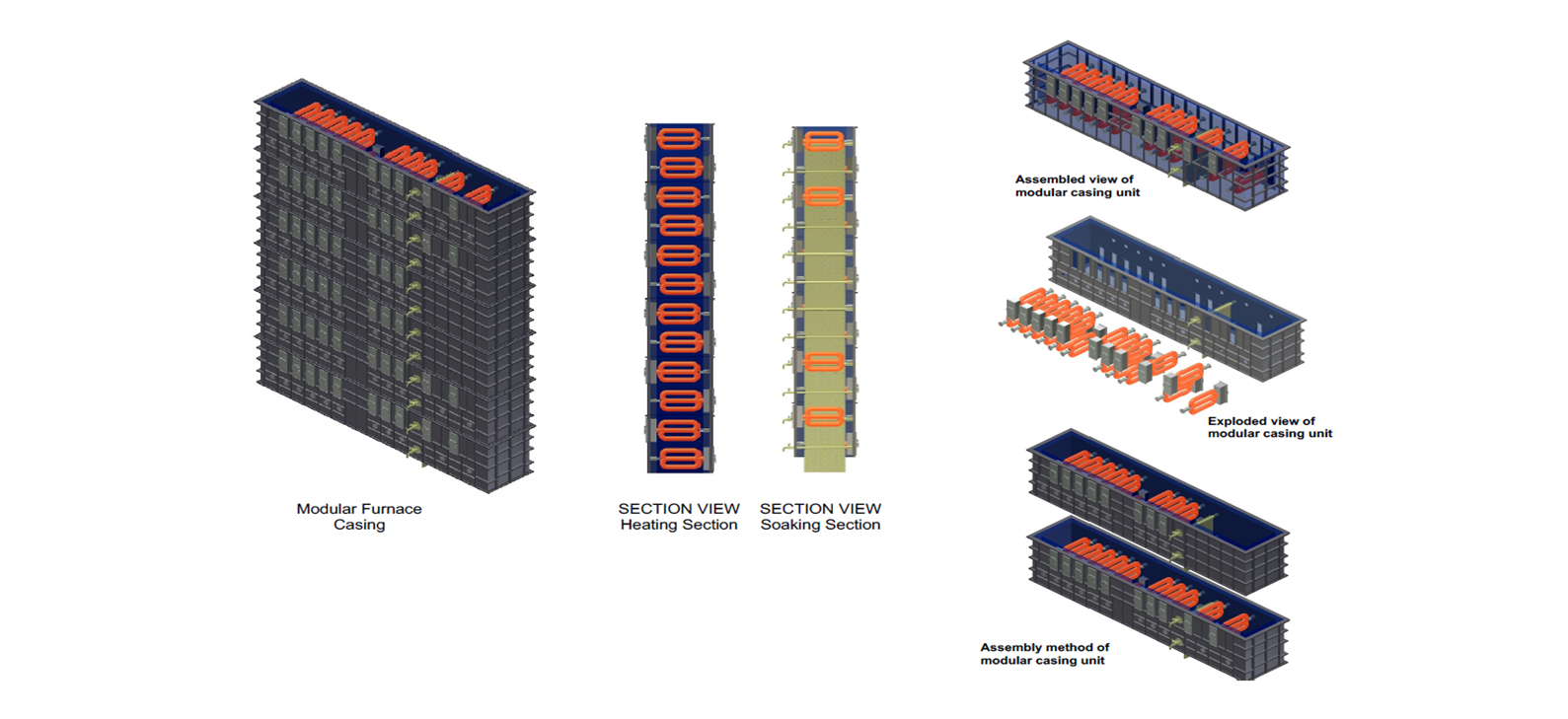
■ Main Parts Details
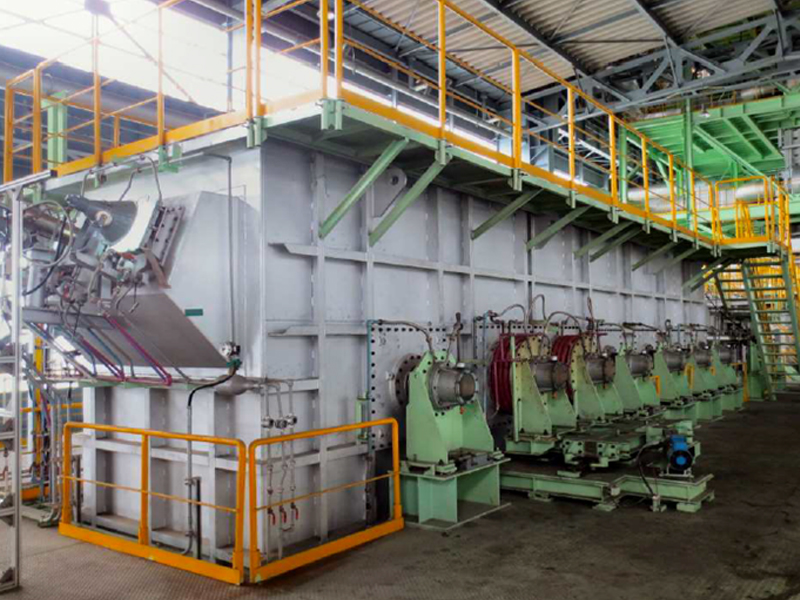
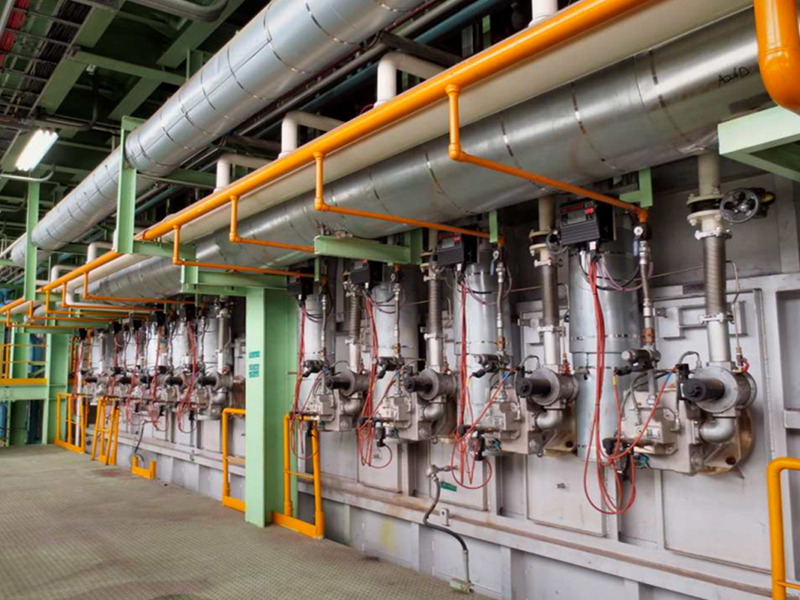
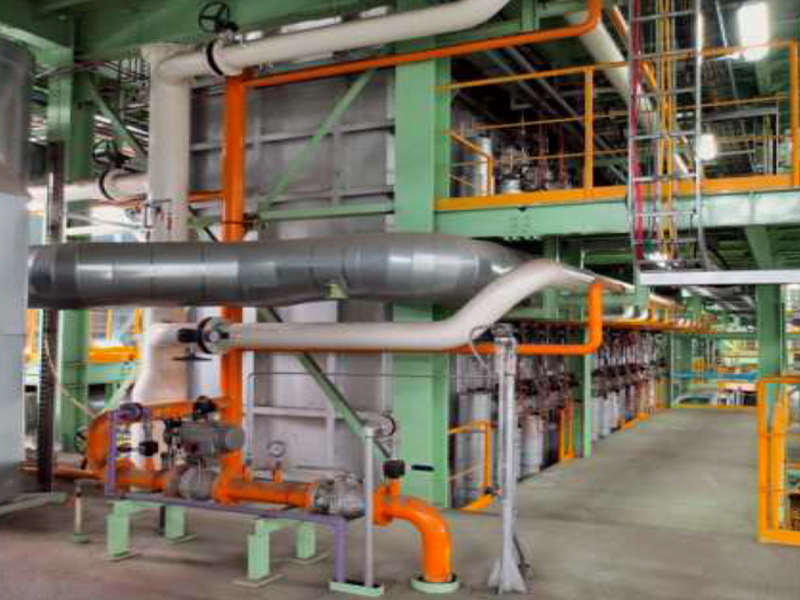
Snout
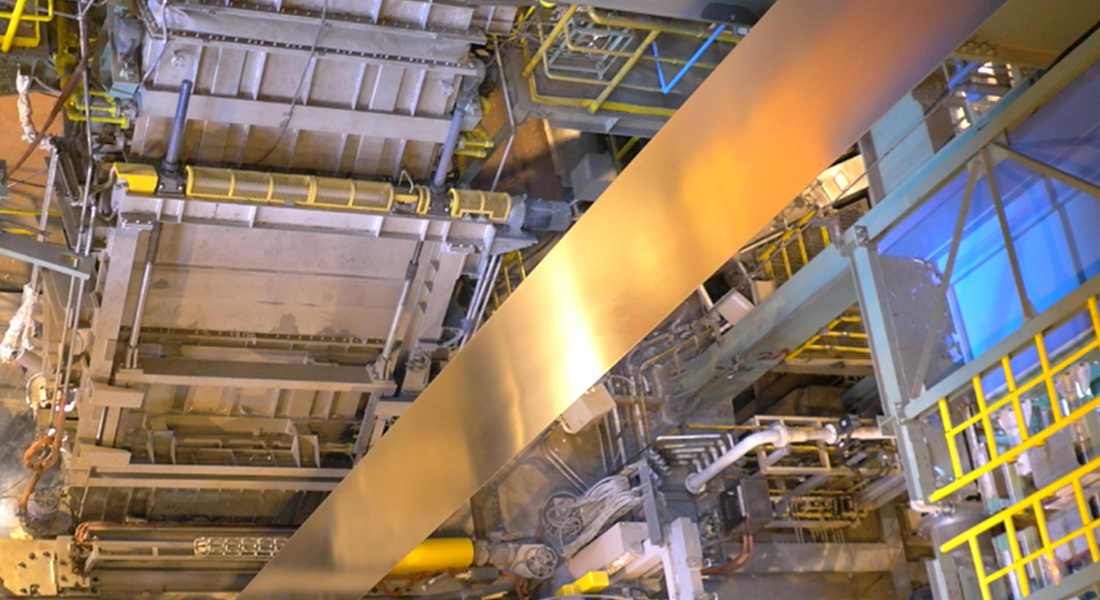
■ Product Description
The snout facility is a passage where, after the annealing furnace, the materials are guided into the plating bath without external contact. In the snout, there are dross, ashes generated in the plating bath, and foreign substances adhering to the surface of the strip. It is crucial that cleanliness is maintained inside the snout because it causes problems in steel sheet quality.
■ Main Parts Details
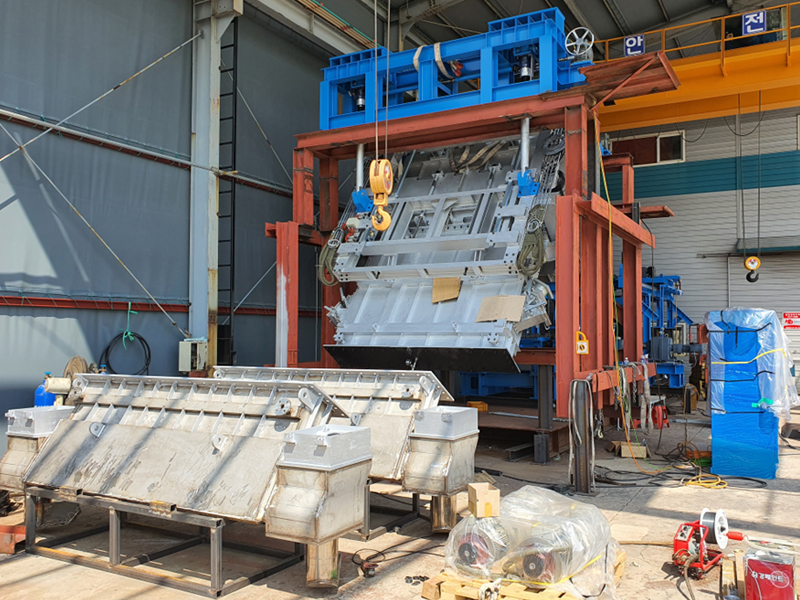
Lifting Device
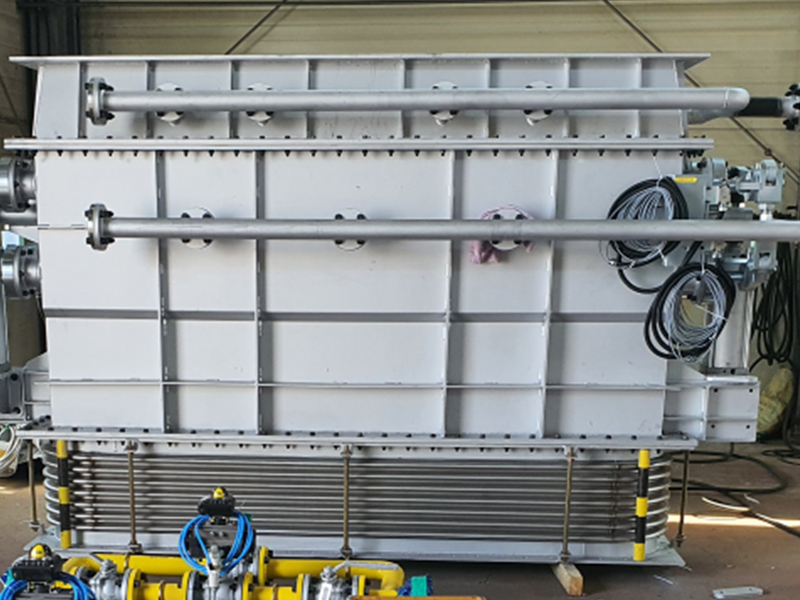
Expansion Joint
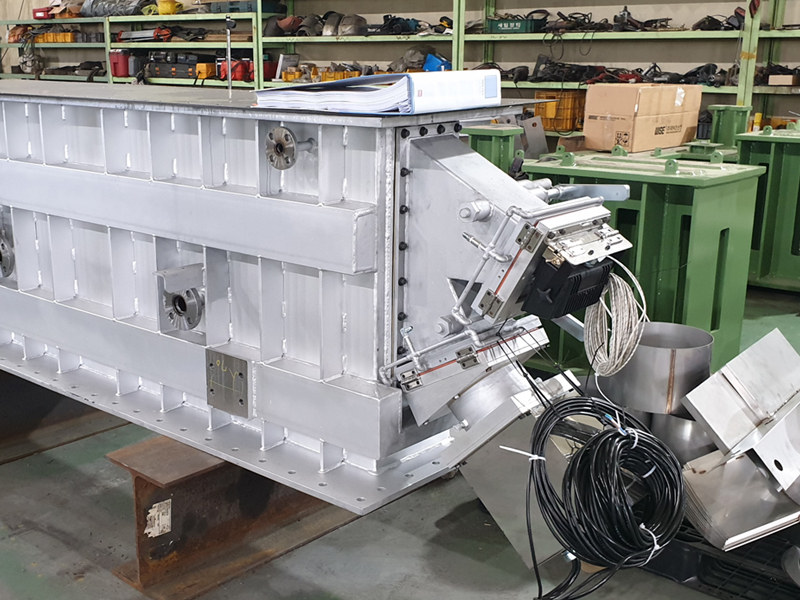
Monitoring System
Wet N2 System
Dross Removal
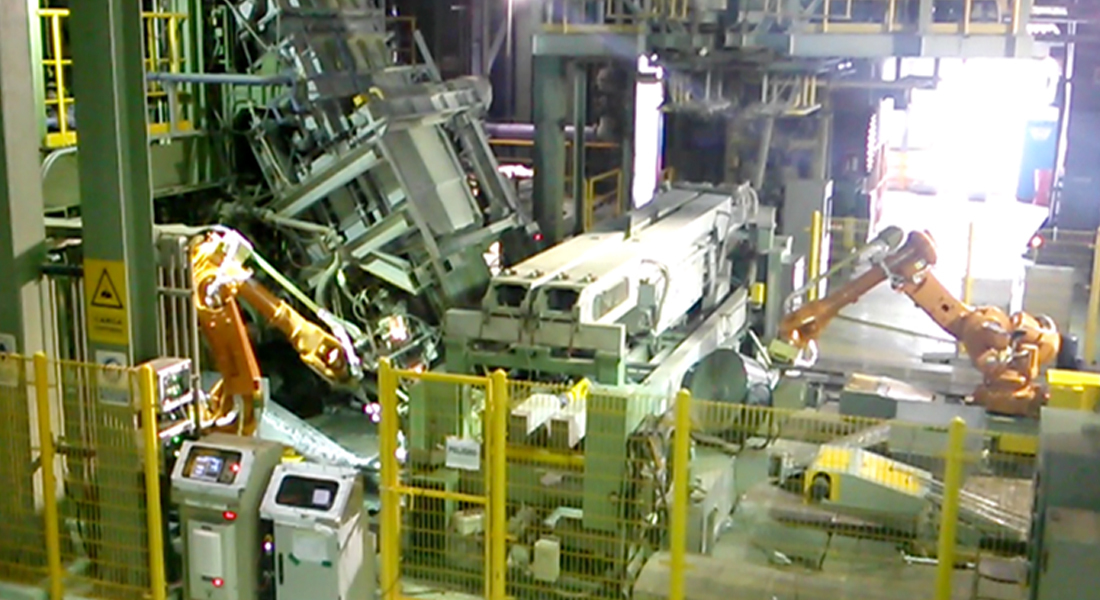
■ Product Description
Standard
6 - Axis Robot / Shovel Clamp Tools / Dross Box / Shovel Stand / Control Panel / Safety Fence
Option
Robot Carriage / Dross Box Carriage / Sampling Spoon & Stand / Emergency Ingot Feeder / Electric Lift for Dross Box Draw
Position of Top Dross Removal Robot
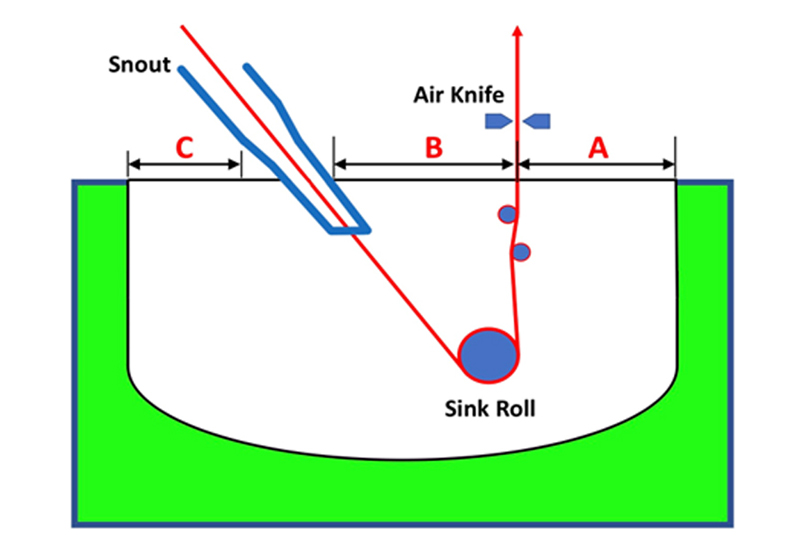
Mandatory : A Zone
Optional : B & C Zones
A & C Zones : Robot Type
B Zone : Top Skimmer
(Under-Development)
Top Dross Removal Robot System
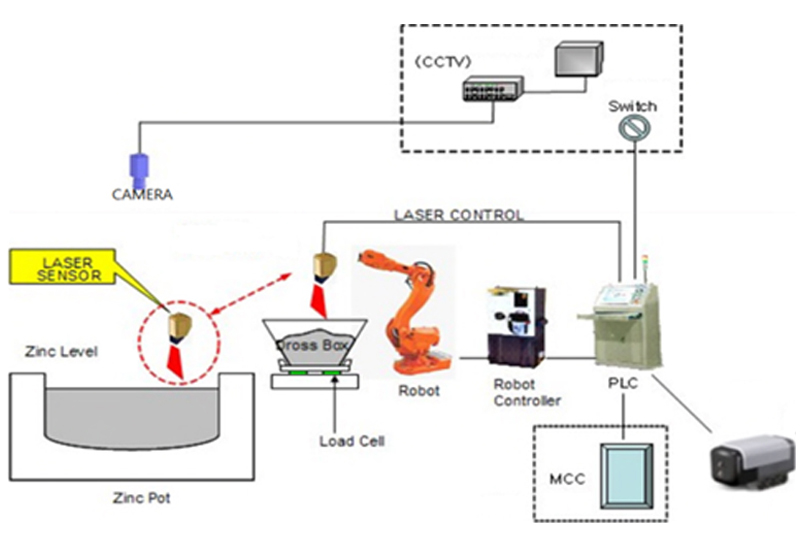
■ Main Parts Details
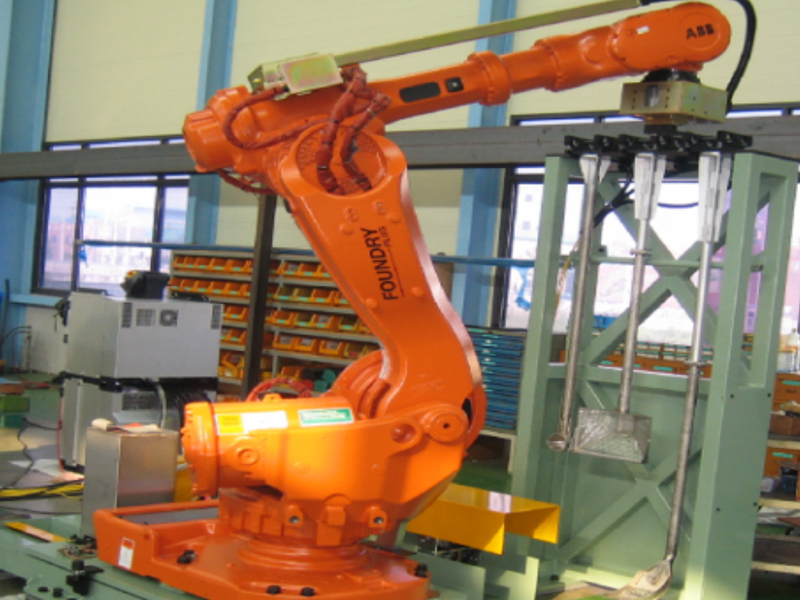
Pot
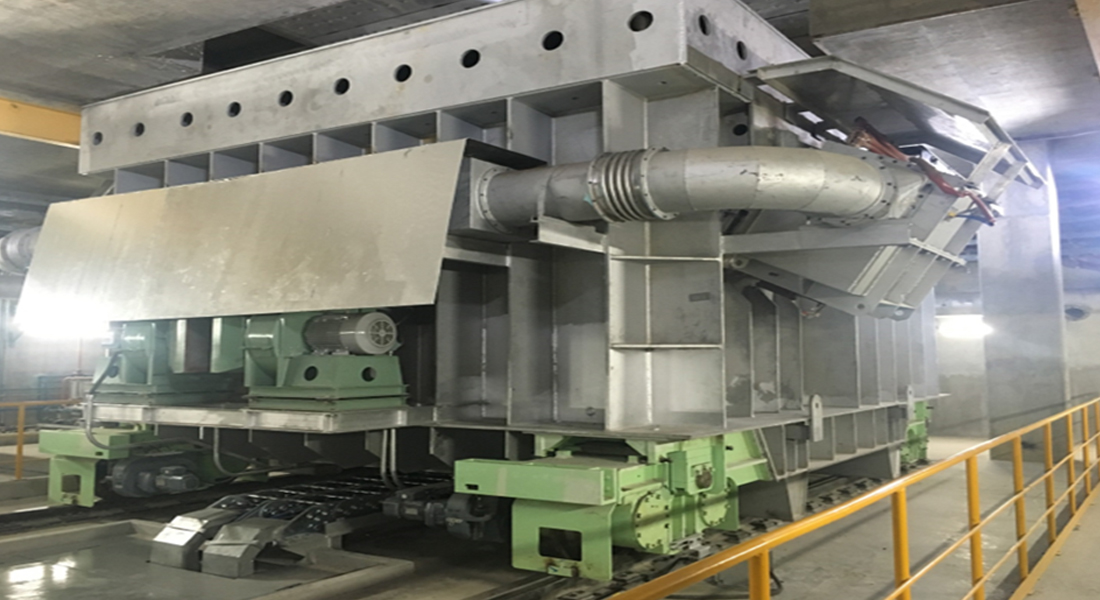
■ Product Description
Zinc pot is the equipment to melt zinc and reserve molten zinc to coat the strip that was prepared from the furnace to meet the coating conditions. This equipment is composed of two pots as main pots to reserve molten zinc, which shall be transferred in one direction from GI to Working and Working to GA position with the lifting system and one pre-melt pot.
The temperature control of pots will be adjusted by another main control system. Temperature range of pots must be 440~480°C to assure best coating condition.
Technologies :
- Fixed pot
· Fixed production
· No requirement to change the alloy or coating
· Reinforced base to be mounted directly on customer foundation
- Mobile pot and bogies
· Multiple productions requiring quick change in alloy coating
· Each bogie is attached to the furnace base by means of a fixed pin passing through a bearing carried on the bogie, thus providing fully articulated movements and equal load sharings between the wheels
■ Main Parts Details
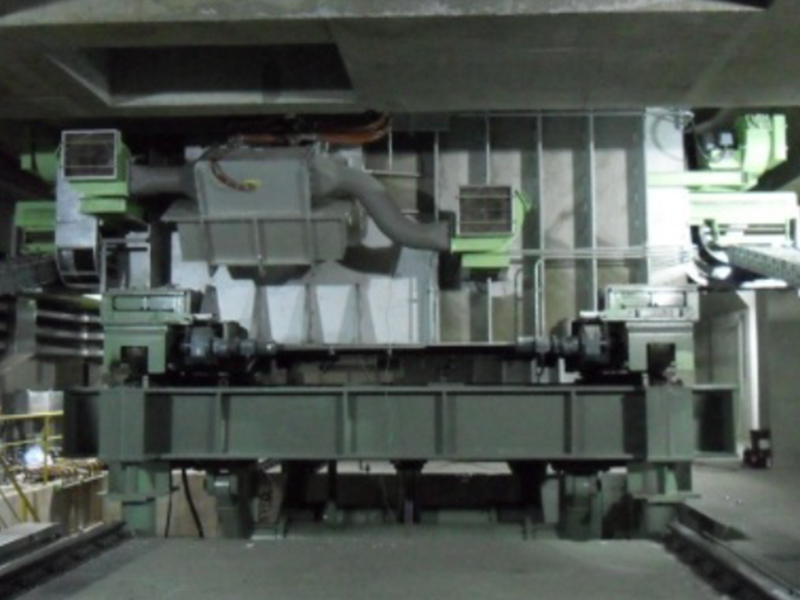
Mobile pot and bogies
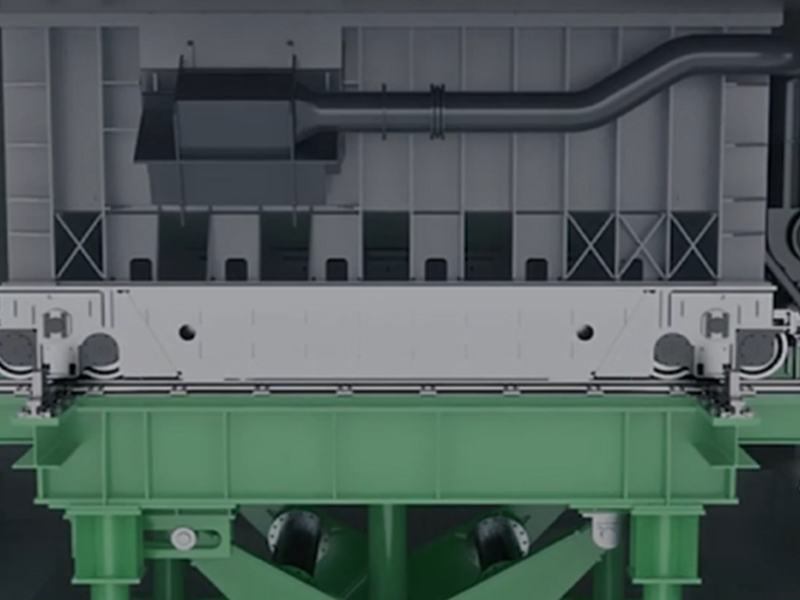
Lift platform
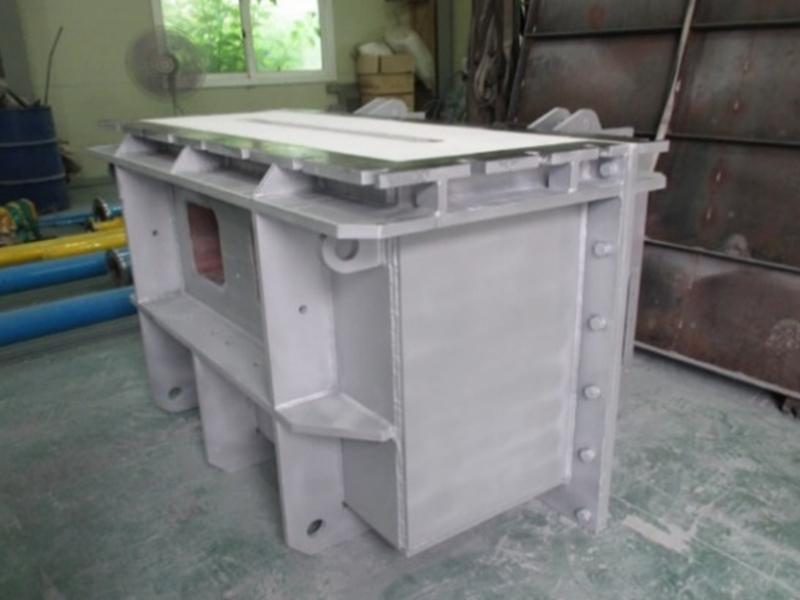
Inductor
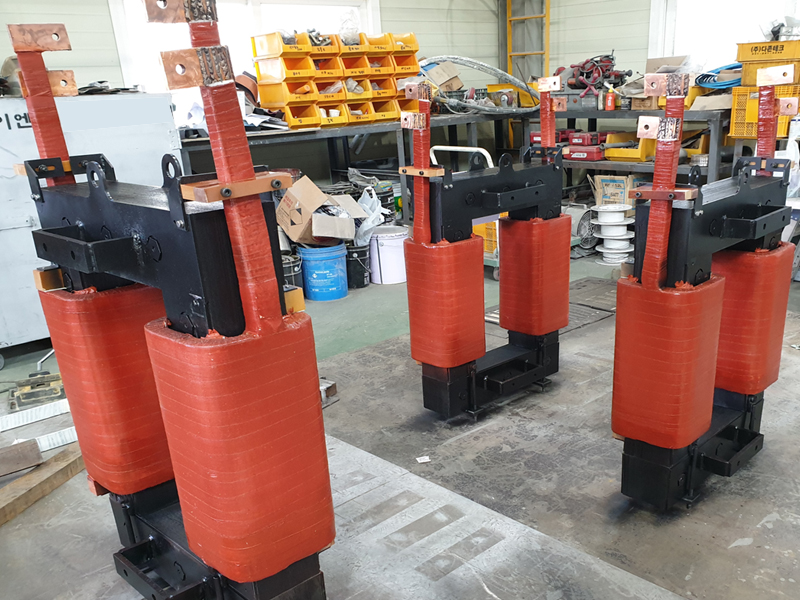
Core & Coil
Cooling Tower
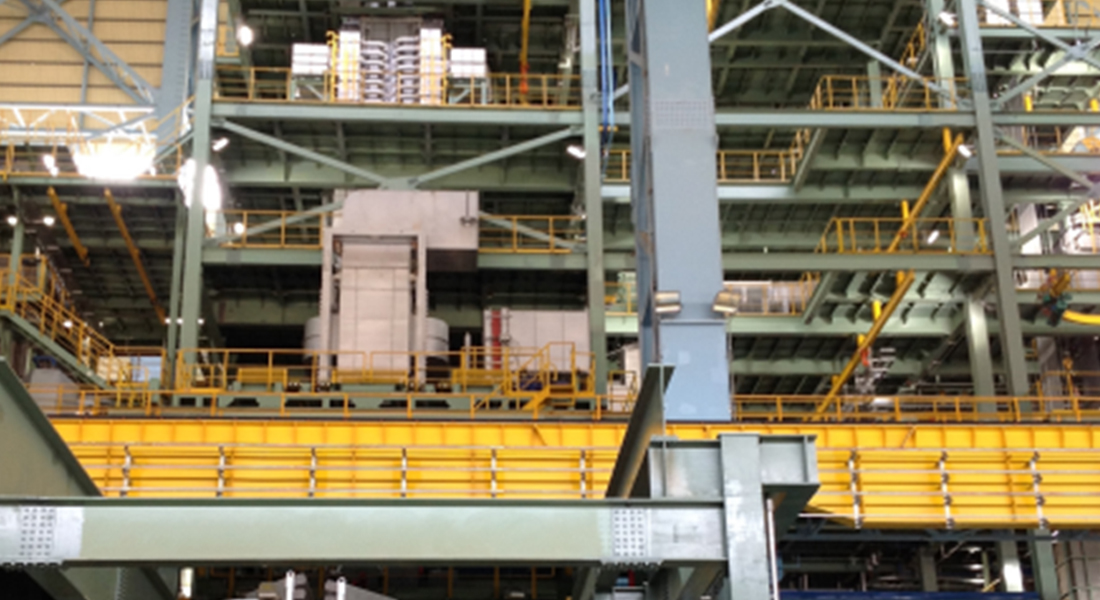
■ Product Description
Cooling tower will be provided for the cooling purpose of the coated strip. After Up pass cooling, the strip is cooled down max. 250℃. After down pass cooling, the strip is cooled down max. 150℃. After final cooling (Water Quench), the strip cooled down max. 40℃.
This item consists of Up pass cooling unit, Top roll, Horizontal cooling unit, Down pass cooling unit, Water Quench unit, and steering roll with CPC.
■ Main Parts Details

Fog Spray Cooler
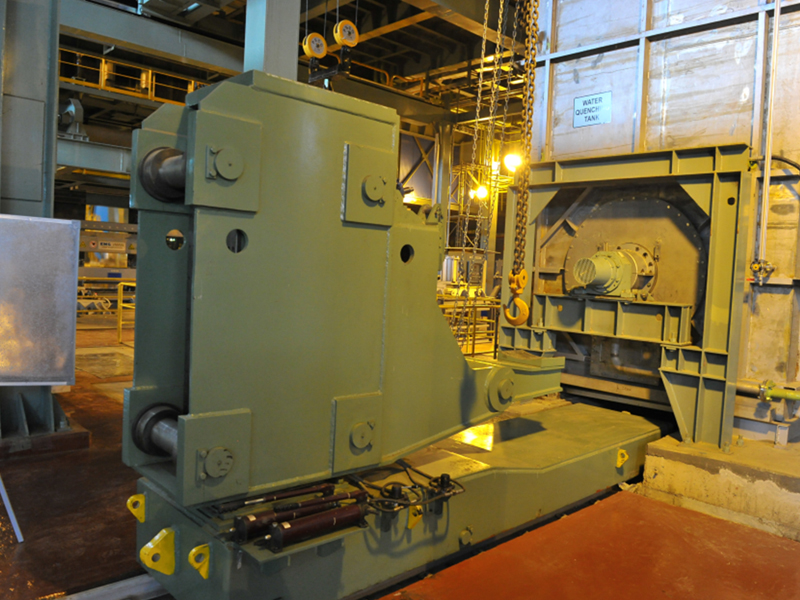
Water Quench
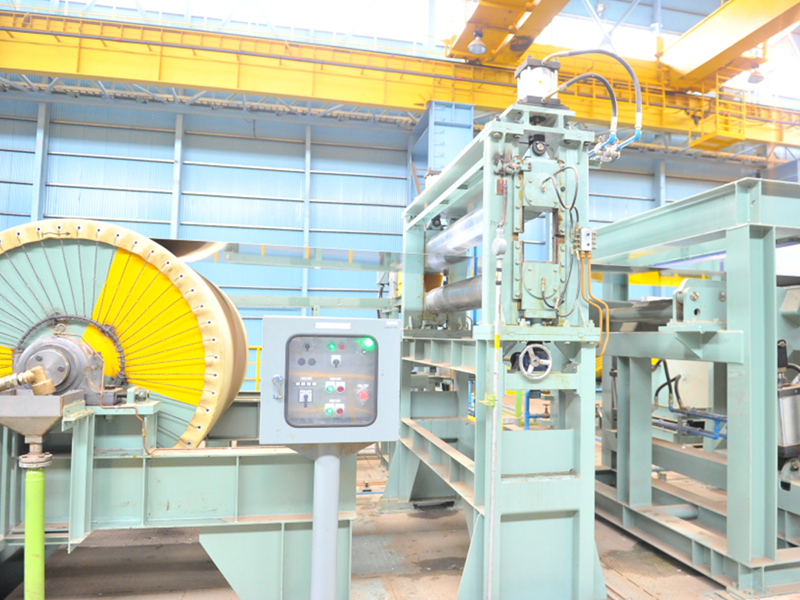
Top roll & Clamp
Skin Pass Mill
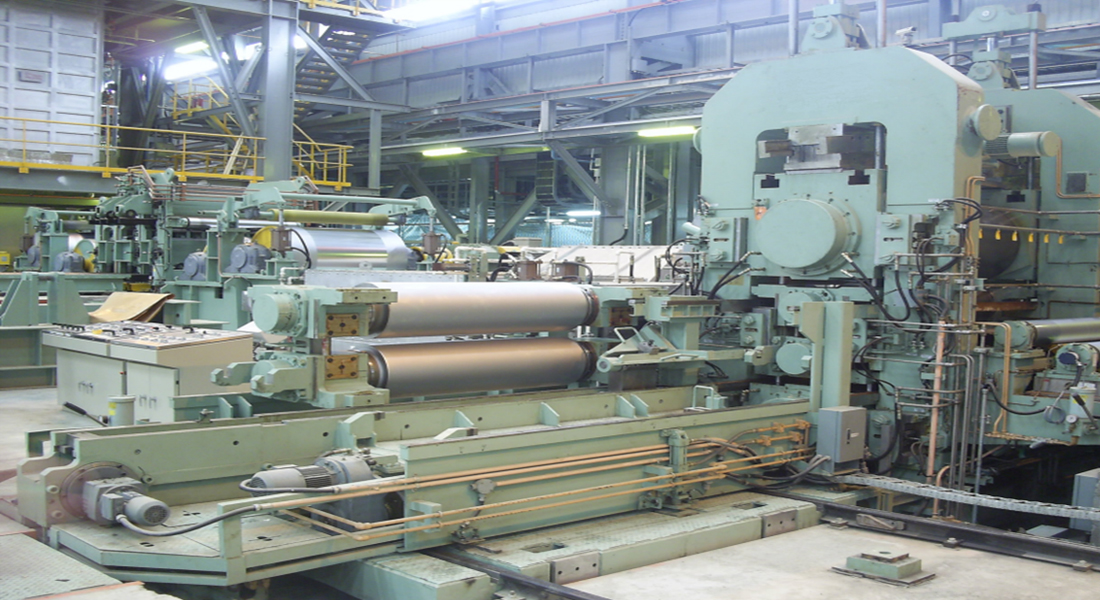
■ Product Description
SPM Performance Quality
- Enhancing of Mechanical Properties
- Adjusting Roughness Requirements
- Improving Strip Flatness
Technologies :
- High precision Roll Force Control System
- Servo Hydraulic System with high-accuracy positioning and pressure control
- High Durability and anti-Vibration Structure Design
- Fixed Roll Alignment Mechanism
- Quick and Easy Roll Changing System
- Optimal operational Data Base
- Application of state-of-the-art Roll Cleaning Device
■ Main Parts Details
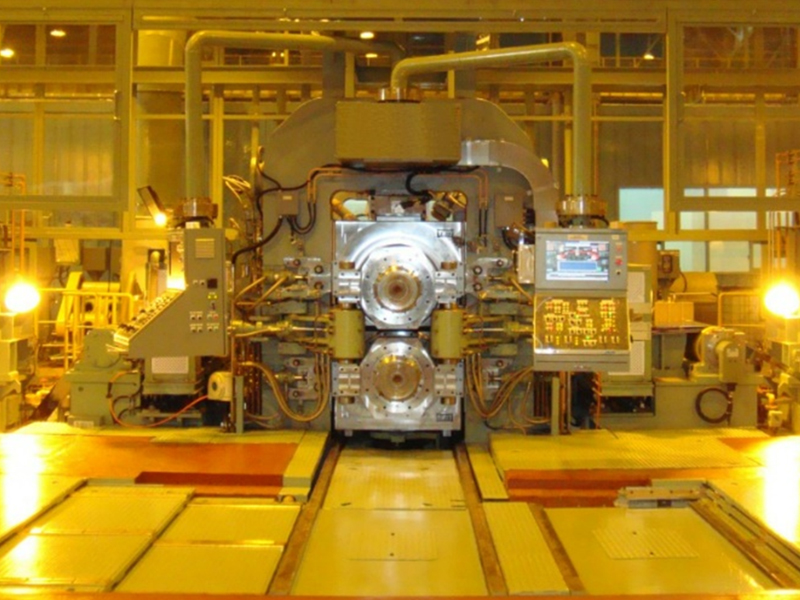
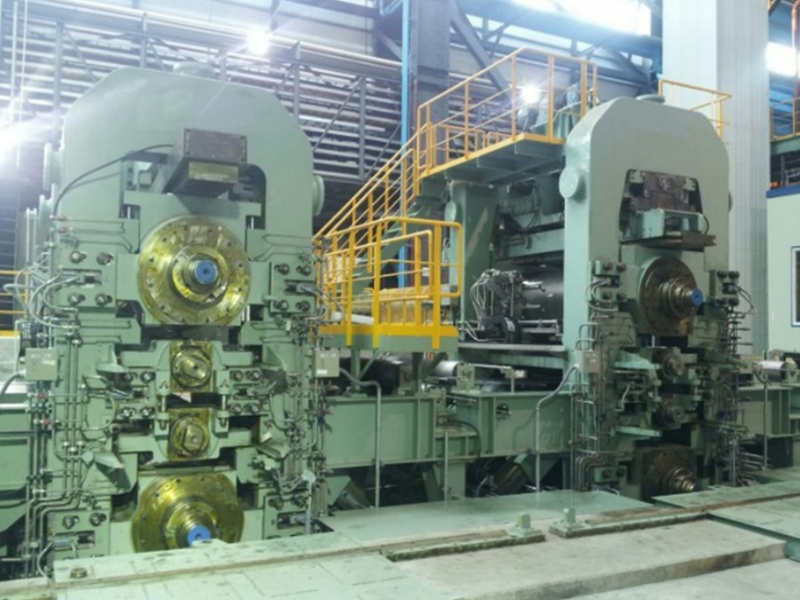
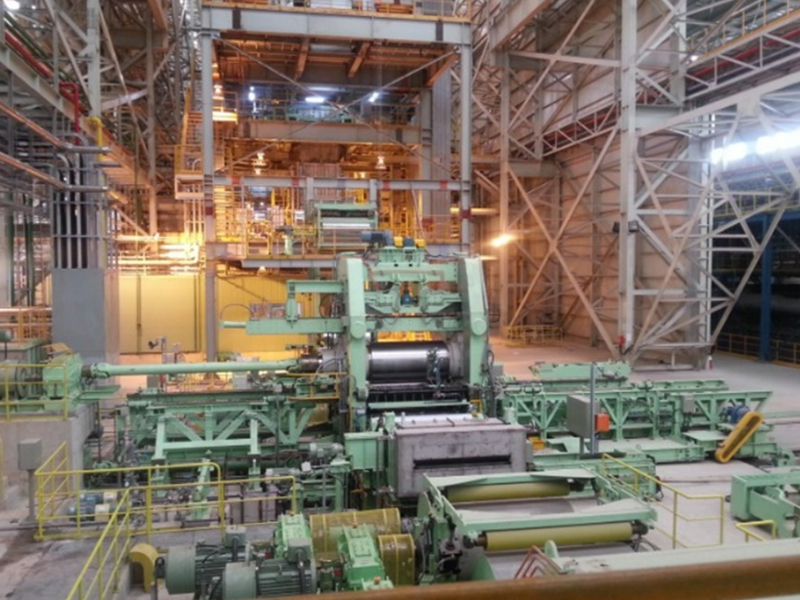
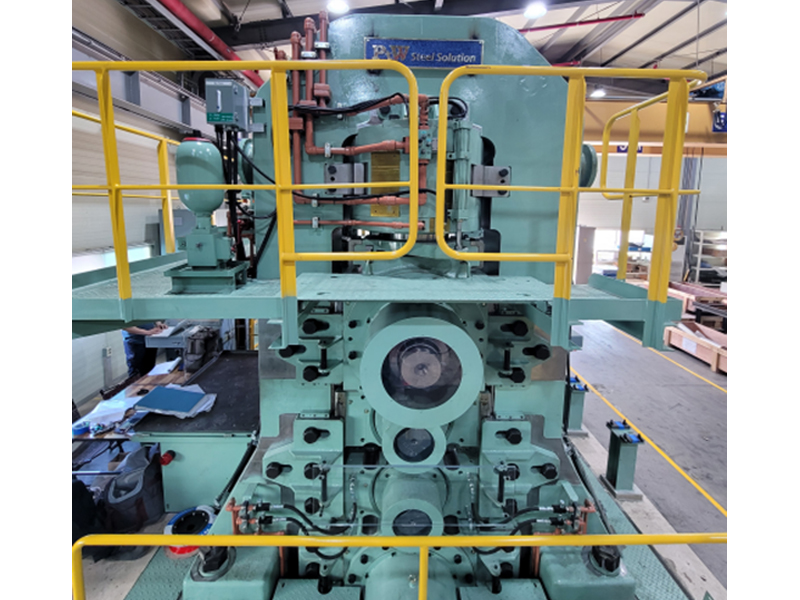